Case Study on Advanced Separation Techniques used in Alkali Leaching-based Mineral Processing Plant
Synopsis
Pressurized alkali leaching inside autoclaves is the main chemical process of mineral processing plants. Leaching is the process, where solute becomes detached or extracted from its carrier substance through a solvent at standard operating conditions. A series of unit operations and unit processes are involved in the extraction of ore i.e. crushing, grinding, dewatering, filtration, leaching, clarification, precipitation, drying, etc. Advanced separation techniques are used in the entire process of extraction of minerals from ore and converting it into the desired product. Two major types of leaching performed in India for ore processing are acidic atmospheric leaching and alkali-pressurized autoclave leaching. The selection of leaching is based on the characteristic of the ore. The authors have working experience in a few advanced uranium ore processing units in India. Some unit operates based on pressurized alkali leaching whereas few units are operating based on acidic atmospheric leaching. Drum filters are used for filtration. Ion exchange (IX) is used for increasing mineral concentration. IX is a reversible interchange of one kind of ion present in an insoluble solid with another of like charge present in a solution surrounding the solid with the reaction being used especially for the separation of solute of importance. It is one of the major processes of ore processing units. Dewatering is done through sedimentation and filtration via high-rate thickener (HRT) and horizontal vacuum belt (HBF) filters respectively. HBF and precoat vacuum drum filters are used for the separation of solids and liquids. In the case of chemical operations - the run of mine ore is crushed in three stages and wet grinding in two stages is done for achieving mineral liberation size (74 microns). Subsequently, HRT and HBF are used in getting optimum pulp density for autoclave leaching, pressurized by oxygen in the presence of lixiviant (Na2CO3 & NaHCO3). Post-leaching is also performed by HBF followed by precoat filtration to get clear mineral-bearing filtrate subjected to precipitation by the addition of NaOH with mineral concentration spiking with the stock solution for achieving maximum precipitation efficiency. The precipitate is thickened, washed in HBF, and dried in a spray dryer. Leached solid is disposed of in an impervious clay layer of 1-meter width with a 1.5mm HDPE sheet. The product barren is carbonated and recycled in a grinding circuit.
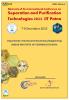

This work is licensed under a Creative Commons Attribution-NonCommercial 4.0 International License.