THE PROS AND CONS OF AN ENERGY-EFFICIENT Q&P APPROACH TO DEVELOP ADVANCED STEELS
Synopsis
The development of steels with increasing strength levels while retaining a sufficient ductility and toughness has been the major focus area of research in recent times. This can be achieved by (i) addition of alloying elements in greater amounts, ex. TWIP and austenitic stainless steels, (ii) optimization of processing parameters, (iii) employment of novel processing route, etc. The higher alloying additions lead to increased cost of the steel, in addition to the issues in casting, rolling, welding, fabrication, etc. Therefore, it is of significant importance to achieve higher strength levels in low alloy steel compositions with the help of novel processing routes. One such approach can be the quenching and partitioning (Q&P) process on low alloy steels, which leads to the stabilization of retained austenite in a martensitic matrix. Some of the recent studies have also shown the presence of bainite and carbides, in addition to the retained austenite and martensite, leading to a multi-phase microstructure at room temperature.
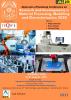

This work is licensed under a Creative Commons Attribution-NonCommercial 4.0 International License.