OPTIMIZED DESIGN AND PERFORMANCE TESTING OF A 1.5 MW WIND TURBINE BLADE
Synopsis
This paper aims to provide a method that can enable designers to deepen their understanding of the dynamics of the design space and to find a blade design that has a low energy cost. In this paper, S818, S825, and S826 series are used for designing wind turbine blades. These airfoils have many advantages in terms of design level, off-design capacities, and structural properties to meet the inherent requirements of wind turbines. The initial design of a 1.5 MW composite wind turbine blade is first designed in this paper using the base airfoil. A multi-objective genetic algorithm has been used for the optimization of S818, S825, and S826 airfoils to achieve two goals – maximum lift and maximum elevation to drag ratio. It is shown that the multi-target genetic algorithm can yield superior airfoils in comparison with the original airfoils. Optimized airfoils are then used to develop a new wind turbine blade. The commercial computational fluid dynamics software has been used for measuring the flowfield and investigate the performance parameters. For the aerodynamic, structural design, and optimization of wind turbine blades, this study is significant.
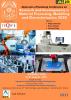

This work is licensed under a Creative Commons Attribution-NonCommercial 4.0 International License.