OPTIMIZATION OF EDM PROCESS PARAMETERS BY USING HYBRID METHODS
Synopsis
In present situation, Aluminium matrix boron carbide (AL-B4C) MMC plays an important role in aerospace, biomedical, nuclear power plants, automobile and automotive industries. In order to do machining on these materials, convectional machining methods are not suitable, because of high tool cost and high tool wear. Due to these reason Advanced machining methods are used for machining AL- B4C material i.e., EDM, ECM, LBM etc., out of these machining methods EDM is one the best unconventional machining process to machine such components. EDM processes which are worked by repetitive sparks between tool (electrode) and work piece based on material erosion. In order to produce the spark in between tool and work piece must be of a thermal conductivity nature. A slight pulse discharge between work piece material and instrument occurs a small distance by melting and vaporizing eliminates the material from the work piece. MRR, TWR & Ra play an important role in the machining process. The present research uses Hybrid methods are used to optimize the process parameters of EDM on AL- B4C metal matrix composite material. The main objective of this work is to decrease the wear rate of the tool and improve the material removal rate with the product having good surface quality.
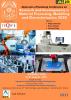

This work is licensed under a Creative Commons Attribution-NonCommercial 4.0 International License.