ENHANCE THE PRODUCTIVITY THROUGH INFLUENCING PARAMETER OF REDUCTION OF COKE RATE IN A BLAST FURNACE
Synopsis
The aim of this paper is to enhance the productivity of Blast Furnace (BF) through influencing some input parameter like hot metal temperature, High top pressure, oxygen enrichment, Coal dust injection, Burden distribution, Burden preparation, percentage Sinter in burden etc. of reduction of coke rate for balancing the customer demand of steel. The Soul objective of this observation for enhance the productivity, reduce the production cost of hot metal through reduction of coke rate, where coke is a utmost important input factor of blast furnace which accounts for around 60% of hot metal cost. Nowadays the world class blast furnace operation needs the highest quality of raw material, smooth operation, and operators. Coke is the utmost important raw material fed into the blast furnace in term of its effect on blast furnace operation and hot metal quality. The high quality coke should be able to support a smooth descent of the blast furnace burden with as little degradation as possible while providing the lowest amount of impurities, highest thermal energy, highest metal reduction and optimum permeability for the flow of gaseous and molten products. They represent of high quality coke to a blast furnace will results in lower coke rate, higher productivity and Lower hot metalcost.
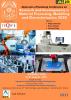

This work is licensed under a Creative Commons Attribution-NonCommercial 4.0 International License.