Computational modelling of In-process mitigation technique to control residual stress in thick plate welding
Synopsis
Fusion welding induces sudden thermal alteration in the small weld region which leads to residual stresses and deformations in the weld joint under the effect ofsurroundingconstraints of parent metal. This residual stress becomes more complex in thick plate weld joints. In the current study, an in-process mitigation technique has been suggested and FE modelled for a thick AISI304 steel plate submerged arc welding. A static heats ink source and a transient side heating source were employed as a combined thermal tensioning unit. In FE modelling, a 3D volumetric heat source (welding), element birth and death technique, surface heat source (side heating), high convection heat coefficient (heat sink) and temperature dependent material properties were incorporated. The effect of individual thermal tensioning source, side heating location, intensity of heat sink and combined heat sink and side heating were analysed for welding induced residual stresses and deformation. It was observed that transient side heating process diminish the cooling rate of the weldments and also reduces the thermal gradient which elevates the compressive residual stress distribution in the heating region to tensile nature. This sudden lift in stress values from compressive to tensile omits the abrupt change in residual stress distribution across the weld centerline which leads to less deformation of the weld plate. Similarly, the heat sink process was observed to decrease the peak temperature in the region away from welding torch. The lower peak temperature induces tensile stress during the welding which decreases the overall compressive residual stress in the region. Hence, the overall peak of the residual tensile stress in the FZ gets decreased. It was observed that the high intense heat sink causes better reduction in residual tensile peak in the weld fusion zone region. The variation in the thermal profile for three different thermal tensioning cases have been shown in Fig.1.The change in longitudinal residualstress distribution for above mentioned cases is also shown in Fig.2. Consequently, it is observed that the combined heat sink and side heating process is an effective in-process mitigation method to control residual stress distribution in thick platewelding.
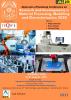

This work is licensed under a Creative Commons Attribution-NonCommercial 4.0 International License.