INNOVATION IN OPTIMIZATION OF MIXING AND NODULIZING DRUM FOR REDUCING ENERGY CONSUMPTION AT SINTER PLANT, TATA STEEL
Synopsis
Sinter Plant is an energy intensive unit in any integrated steel plant. Along with solid fuel like coke breeze, electrical power consumption contributes to a major portion of energy consumption in iron ore sintering process. There are several high electrical-power consuming equipment in a sinter plant. This provide immense opportunity to optimize these equipment to save electrical energy. Mixing and nodulizing drum (MND) is one of the high electrical-power consuming unit and is used for mixing of base mix with trimming flux and solid fuel along with calcined lime and water. Mixing and Nodulizing Drum (MND) enables increase in mean size of sinter mix due to ball formation during its rotating movement and higher mean size of sinter mix increases sinter bed permeability which leads to faster sintering and higher sinter machine productivity. Several innovative experiments were conducted at Sinter Plant (SP) 3 of Tata Steel Jamshedpur to optimize the speed of MND to save electrical energy without effecting sinter plant productivity and product sinter quality. At sinter plant, Mixing and Nodulizing Drum (MND) generally rotates at fixed RPM (rotation per minute). At SP3 MND run at constant RPM 1400. So, there is possibility to reduce RPM to increase retention time of sinter mix inside MND which may improve sinter mix Granulation Index (GI) which is an indicator of balling efficiency of MND. To establish this, a variable- voltage/variable-frequency (VVVF) drive installed in MND at SP3 and experiments were conducted with reduced MND RPM to improve GI and saving of electrical power energy. Very encouraging results are obtained with reducing of RPM of MND at SP3 in terms of saving electrical energy by ~40 kWh/t and improvement in GI of sinter mix by 3-5 points which finally helped higher sinter machine productivity by ~1 t/m2/d with good sinter quality. This paper elaborates the saga of venturing in to the next level of initiatives to reduce energy consumption in an integrated steel plant which will have long term impact on reducing carbon foot print and environment conservation.
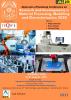

This work is licensed under a Creative Commons Attribution-NonCommercial 4.0 International License.