FLUX INJECTION THROUGH TUYERES IN BLAST FURNACE
Synopsis
An appropriate slag formation is a precondition for getting a smooth operation of the blast furnace and a good quality of hot metal. It includes dissolution of the gangue of iron bearing materials and ash of fuel & fluxes into a liquid slag properly with desired slag properties. Cohesive zone has the highest resistance to the gas in the blast furnace, its shape and thickness normally determine the gas distribution. If the slag volume at the cohesive zone can be decreased and the slag properties can be improved significantly, the productivity of blast furnace could be increased accordingly. Physically, the burden, except for coke, transforms gradually from solid state-soft-semi-melt and finally into complete molten state. During the process, voidage of the burden decreases making its permeability worsens. Chemically, the composition of the slag formed depends on not only on the compositions of the burden charged, but also on the reduction degree of the iron bearing materials at the cohesive zone and dissolution of the burden materials charged. Reduction of iron oxides remained in iron bearing materials proceeds at much faster speed at cohesive zone than in lumpy zone.
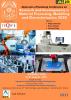

This work is licensed under a Creative Commons Attribution-NonCommercial 4.0 International License.