DISCRETE ELEMENT ANALYSIS OF GRAVITY-DRIVEN POWDER FLOW IN COAXIAL NOZZLES FOR DIRECTED ENERGY DEPOSITION
Synopsis
Directed Energy Deposition (DED)is a Metal Additive Manufacturing (MAM) technique prominently used for the manufacturing of large scale parts, component restoration, and surface cladding. DED uses a focused heat source to create a melt pool on the substrate, into which ‘build’ material is injected. This leads to growth in volume and mass of the melt pool, which, upon solidification, results in a deposited track. Delivery of powder feedstock into the melt pool can be accomplished using several methods. A pneumatic system, which uses inert carrier gases for powder feedstock handling, is the most common design. However, a pneumatic system is often associated with high particle velocity leading to reduced catchment efficiency, poor surface finish, and increased porosity, thus, resulting in poor part performance. A gravity-driven nozzle alleviates these limitations by eliminating carrier gases, which not only makes the process more efficient but also economical, and sustainable. In this work, a gravity-based, continuous coaxial powder delivery head is studied using the Discrete Element Method (DEM). The results from the analysis suggest favorable powder flow behavior. The simulations are also carried out for various head tilt angles to determine appropriate operating conditions and their effect on powder flow behavior and, consequently, on deposition characteristics.
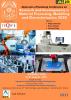

This work is licensed under a Creative Commons Attribution-NonCommercial 4.0 International License.