Phenomenological modelling of surface morphology in friction stir welding of aluminium alloy
Synopsis
The modelling of friction stir welding (FSW) require multi-physics knowledge of material, thermal, and interface behaviours. Several studies have been led to comprehend the underlying physics of the process and thermo-mechanical behavior of the FSW process. The literature primarily discussed about the impact of different process parameters on thermal modelling and its effect on microstructure development. Most of the numerical models developed discussed only the temperature, stress or strain distribution during welding. Be that as it may, these models disregard surface morphology and material movement during the FSW procedure. In our current effort, a fully coupled 3D thermo-mechanical model is developed to anticipate the surface morphology in order to predict the flash formation throughout the FSW process. The impact of different process parameters is contemplated on surface morphology of the weld. Coupled Eulerian-Lagrangian (CEL) method is utilized for viewing the FSW procedure by utilizing commercially available ABAQUS software. The current model is equipped for predicting the material flowing out of the workpiece and thus helps in the visualization of the chip formation and arrangement. The developed model can also be used to visualize the morphology of the workpiece surface, temperature, stress and strain variations.
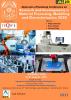

This work is licensed under a Creative Commons Attribution-NonCommercial 4.0 International License.