A STUDY OF MICROSTRUCTURE AND MECHANICAL PROPERTIES OF WIRE ARC ADDITIVE MANUFACTURED COMPONENT WITH ER70S6 ALLOY WIRE USING CMT PROCESS
Synopsis
Additive manufacturing is a very popular word in the present day as various researchers are focused on this field all around the world. Every new researcher coming to this field of additive manufacturing is busy in developing new methods and techniques to make it more versatile and efficient in terms of applicability. Wire arc additive manufacturing (WAAM) process a new addition to the AM processes, is growing rapidly in the field of the metal additive manufacturing process because of its high deposition rate, low equipment cost compared to laser and electron beam, saving lead time, high BTF ratio, no limit on part size and many other advantages.
In this study, a wire arc additive manufacturing system based on cold metal transfer Gas matel arc welding technology was used to fabricate a solid block component with ER70S6 MS alloy welding wire. This study presents the investigation on anisotropy behavior of resulted microstructure and mechanical properties including tensile, impact, and hardness of the manufactured block component. The samples were taken along the parallel and perpendicular to the welding direction. The tensile properties of the samples were found almost uniform in both the directions with values of the ultimate tensile strength (UTS), yield strength (YS), and elongation (%E) were found to be 510 ± 5 MPa, 373 ± 5 MPa and 37% ± 2% respectively. The average Vickers hardness values at 10 kg load in parallel and perpendicular direction were found around 80 kg/mm2 and 72 kg/mm2. The Impact toughness at -30°C was found to be 148J and 170J in the parallel and perpendicular direction. The toughness obtained is much higher than the required minimum impact strength of 80J at the sub-zero temperature as per the AWS requirement for the used ER70S6 welding wire. The microstructure observed in welded samples is ferrite and bainite which consists inside and along the prior austenite grain boundaries. Mostly grains were elongated in the welding direction. From the present work, it is evident that the near-net-shape component fabricated with the WAAM process has quite acceptable mechanical properties without much effect of directionality.
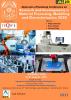

This work is licensed under a Creative Commons Attribution-NonCommercial 4.0 International License.