Underwater Friction Stir Welding of Aluminum Alloy
Synopsis
Friction stir welding (FSW) is one of the most prominent methods of joining similar and dissimilar aluminum alloys. The tool pin profile, force, rotational speed and transverse speed plays a vital role for heat generation and homogeneous mixing of materials during welding and microstructure and mechanical properties are also varied of the same of weld. There is a wide range of application in FSW of aluminum alloy i.e. automobiles, aerospace, shipbuilding, construction etc. Nowadays friction stir welding is performed at different environments such as under water. Moreover, underwater friction stir welding (UFSW) is extensively applied in ship building components and marine structures to enhance the weld joint quality. In recent times friction stir welding is performed in a very cool environment such as liquid nitrogen in order to enhance the weld joint quality. This paper summarizes the advances and challenges of submerged friction stir welding at different environment. The current work also encompasses the variation of tool pin profiles for welding Al 2024 aluminum alloy underwater and in air. In under water friction stir welding (UFSW) heat become more concentrated under the tool and cooling rates are higher due to water environment which ultimately boost up the mechanical properties of the weld joint. However hard and brittle precipitates are formed at weld bead due to difference in peak temperature of UFSW compare to air friction stir welding (AFSW) made it more challenging. The square tapered pin profile shows higher tensile strength as compared to the other pin profiles.
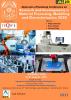

This work is licensed under a Creative Commons Attribution-NonCommercial 4.0 International License.